Many buildings will have been continuously expanded and redeveloped during their lifetimes. This often results in plant rooms being retrofitted which can mean that there is very little space for plant, never mind professionals who need to access the room to monitor, maintain or replace equipment.
This problem is not just found in older buildings. Plant rooms do not generate value for a developer, so architects are often encouraged to design plant rooms to be as small as possible and ‘out of the way,’ which can mean in some instances they are on the roofs of buildings which means cranes are needed to remove equipment. As a result, plant replacement can become extremely difficult from an operational perspective. Unfortunately, this means that is some instances, sites are often forced to limp along with appliances leaking water and fumes because it is known that replacement is going to be complicated and potentially time consuming. This also means that they must be reactive when issues arrive, and failures occur.
Solutions
One solution is to take a plant room offline by using a temporary solution allowing any work to be done and equipment fixed or removed and replaced with hardly any downtime. To break down a boiler and re-build it in a plant room is a hugely expensive operation and many manufacturers will not even allow this. There is also often not enough allowance made be architects to get equipment out, whilst leaving everything else in situ.
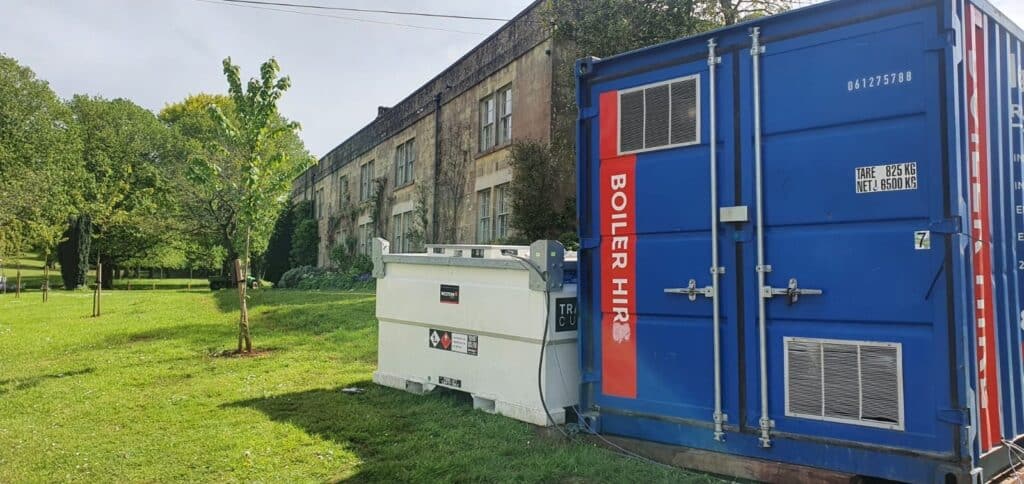
Working on live systems also increases the risk of worker injury. Working on any live system is dangerous, it is safer to work in a plant room that is cold and has its power isolated because otherwise one error can have fatal consequences. Of course, strict safety measures are put in place but you can never account for human error so there is always a residual risk, by using a temporary boiler you can eliminate that risk. If something were to go wrong whilst working on a live system a building could be forced to shut down completely which in certain industry sectors could be catastrophic.
By taking plant offline and using temporary solutions people can save time and money in the long run. On a large site where there may be underground pipework which can be difficult to get to, it is possible to breakdown the loads to take the site on and offline, helping to maintain the system and avoid having to turn off large parts of the network. This allows people to keep their buildings running.
Monitoring first
Inefficient boilers can cost a lot more than the cost of a new boiler in the long term if it is badly maintained. I always recommend monitoring as a first cause of action. People should have heat meters on their appliances to monitor the efficiency of their plant. They should also have a planned maintenance schedule and a planned replacement schedule in place. There should also be a plan just in case plant fails completely; it should identify where temporary plant can be safely sited. This will reduce the time it takes to put in temporary measures and avoid delays getting buildings up and running again.
Monitoring shouldn’t just be limited to the current plant. Any temporary boiler supplied by Ideal Heat Solutions is supplied and fitted complete with the state-of-the-art BMS Two Way Monitoring system. This allows Ideal Heat Solutions’ engineers to monitor the temporary boiler’s performance remotely which means if any issues arise, they can be taken care of immediately providing peace of mind.
As featured in Modern Building Services, please view the digital archive here: https://modbs.co.uk/news/fullstory.php/aid/19956/Plant_rooms_and_solutions_available_.html
Please click here to contact us about how Ideal Heat Solutions can provide for your temporary boiler needs.